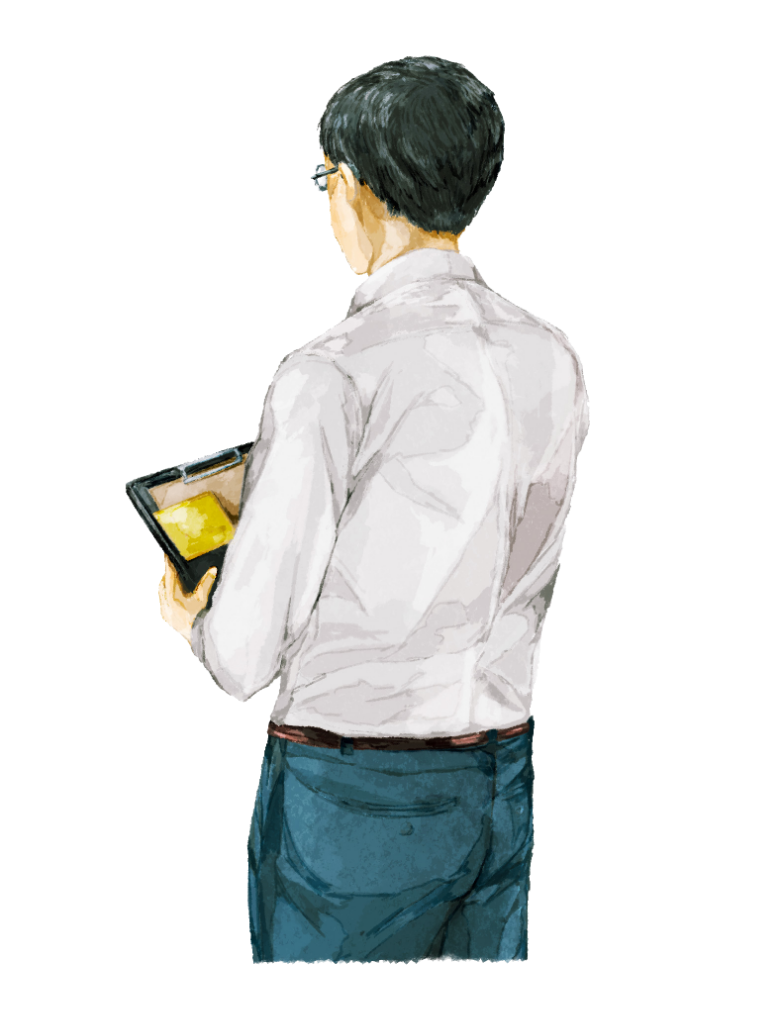
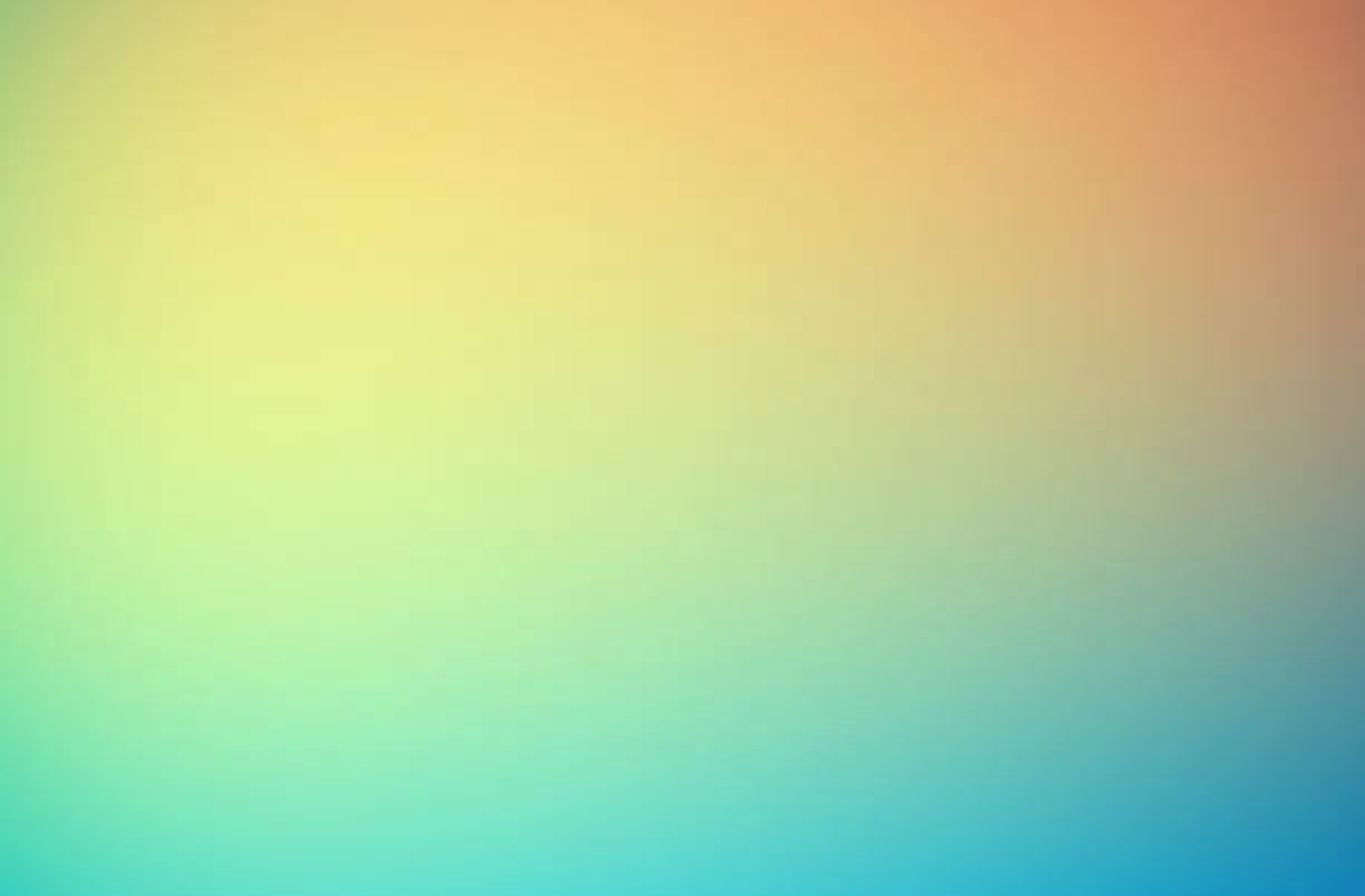
高度な動画撮影が可能なスマートフォンカメラ、自動車の“眼”となって周囲にある対象物の位置や形状を高精度で認識する自動運転のためのカメラ技術、工場や店舗で人やモノの動きや状況をAIで自動検知するカメラ。これらのカメラの多くにおいて「積層型CMOSイメージセンサー」の技術が土台になっています。
前回、ソニーが世界に先駆けて明るくノイズの少ない高画質な裏面照射型CMOSイメージセンサーの商品化を実現し、デジタルハイビジョン“ハンディカム”に搭載されたエピソードを紹介しました。次のチャレンジとして、この価値をより多くの人に実感してもらうため、ソニーは「携帯電話のカメラに搭載できる裏面照射型CMOSイメージセンサーを作る」ことを目標に掲げました。それには、イメージセンサーの携帯電話でこそ求められる小型化や高機能化、低コスト化といったまた新たな山積みの課題が待ち構えていました。
全ての課題と向き合い、あくなき挑戦の結果生まれたのが、積層型CMOSイメージセンサーです。指先に載るほどの小さなイメージセンサーに常識を変えるような可能性をもたらしたこの技術の開発背景には、一人のベテランエンジニアの苦悩と奮闘がありました。

ソニーが裏面照射型CMOSイメージセンサーの開発に成功し、それを実装したカムコーダーを世に送り出そうと奮起していた2008年4月、一人のベテランエンジニアが、CMOSイメージセンサーの開発チームに参画します。ロジックICの量産化技術に長年携わってきたデバイスエンジニアの梅林拓です。
「カムコーダー向けの裏面照射型CMOSイメージセンサーを、携帯電話のカメラでも使いたいと、着任してすぐに上長から相談を持ちかけられました」
当時の携帯電話のカメラは画質が荒く、一般的なデジタルカメラと比べるとかなり感度が低くノイズが目立ちました。携帯電話が人々の生活に浸透するにつれ、もっといろいろなシーンで、思うがまま写真を撮りたくなるはず。そのためにはより良い画質で、どんなシーンでも写真や動画の撮影を楽しめる高機能なカメラが求められることは明白でした。
そこで2010年、ソニーは裏面照射型CMOSイメージセンサーを携帯電話向けにも商品化。しかしながら、当時の技術のままでは、将来的に携帯電話のカメラに求められると予想される高画質化と高機能化の要望は満たせないことは明らかだったほか、従来の携帯電話に使われるセンサーのコストより高価だったという課題がありました。
カメラは、当時からユーザーが携帯電話を選ぶ際の重要な判断要素でした。携帯電話メーカー各社とも、より使いやすく撮影の楽しみ方を広げるカメラの開発、そして端末をいかに手頃な価格帯にもっていけるか、挑戦を続けていました。
さらに、スマートフォンの登場によって、カメラは単に写真や動画を撮影、保存する目的だけではなく、さまざまなスマホアプリと連携してコンテンツを楽しむようなユーザーのニーズにも応えるものでなくてはなりませんでした。
そのためカメラ部品の供給側に立つソニーも、カメラの進化を実現し続けることができる、より安価で、かつ高機能なイメージセンサーの必要性を感じていました。
小さいままチップの機能と画質を高める、しかも工程が増えるのに安く作る
――― これらの要求は普通なら相反するものです。その上、梅林はこれまでイメージセンサーの開発経験がありませんでした。ただ幸いにして、これまでのロジックICの量産化技術で培ってきた知見が生きたのです。
梅林は、量産技術屋らしい発想で、まず最初に小さく、安く作る方法から模索し始めました。
「1枚の半導体ウェーハからたくさんチップが取れるようにすれば安くなるのではないか。すぐにこう発想したんですね」
イメージセンサーのチップは、「ウェーハ」という丸くて薄いシリコン基板から複数枚作り出されます。梅林は、チップ一枚あたりの面積を小さくして一度に取り出せる数を増やすことで、その分デバイスの単価を下げられると考えたのです。
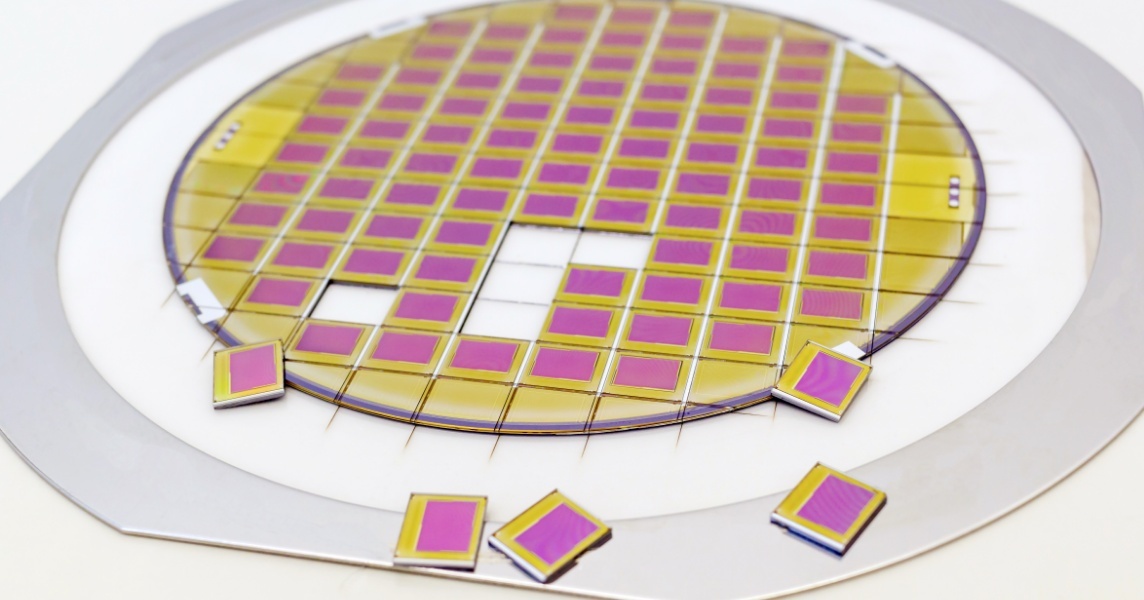
このチップの面積を小さくするため何ができるか―― 。行き着いたのが「積層型」という構造でした。
「もともとは同じチップの面に並べられていた画素部分と回路部分を別々のチップにして、縦積みにする。そうすることで、一つひとつのチップが小さくなる。実際に開発中のイメージセンサーの概略図を使ってポンチ絵を書いてみたら半分ぐらいの大きさになることが分かりました」
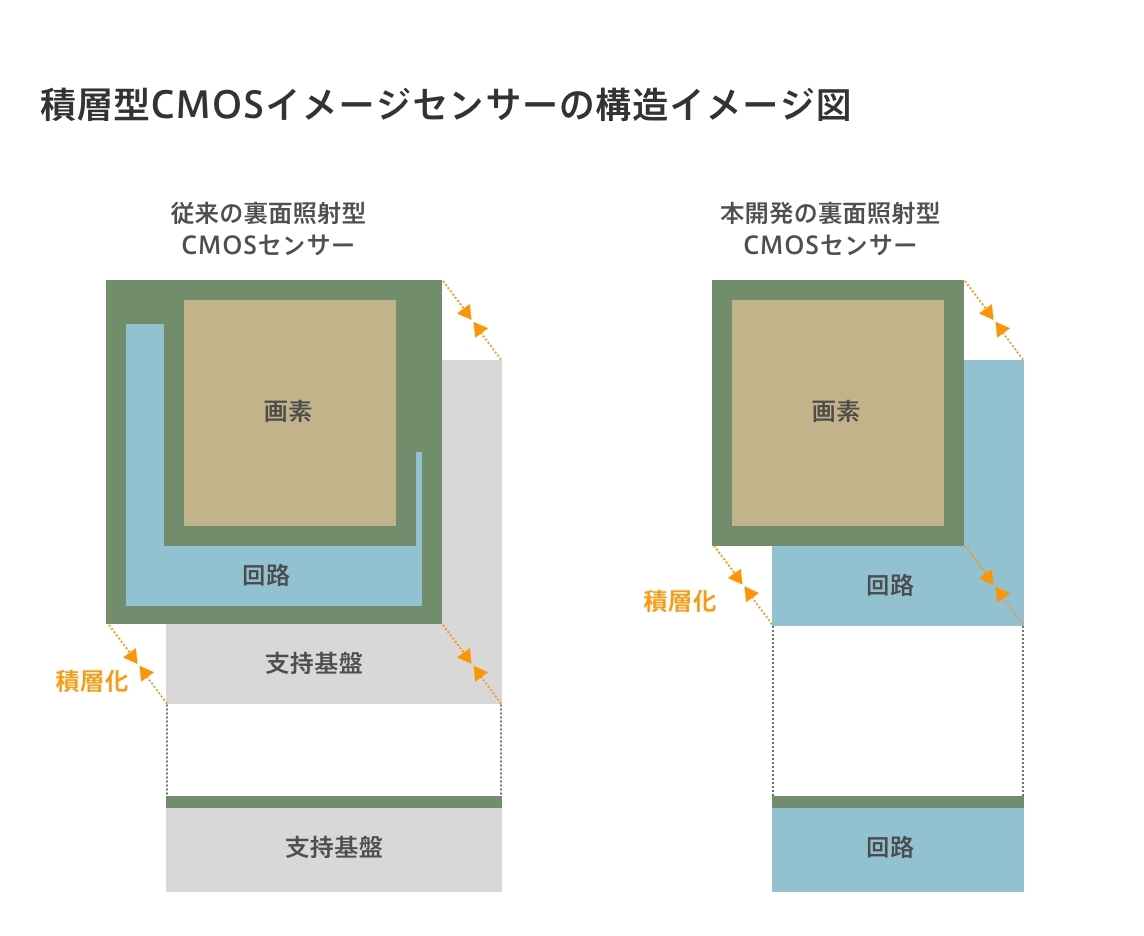
従来の裏面照射型CMOSイメージセンサーは、画素部分と回路部分が一つの層に形成され、その層の下に「支持基板」を貼り付けていました。上の層がペラペラに薄いため、強度を担保するためです。それに対して、梅林が考えた「積層型」は、この支持基板の代わりに回路を形成したチップを使い、画素部分と重ね合わせてしまう構造でした。こうして回路が下の層に引っ越すことで、チップの面積が抑えられます。
もしこの画素部分と回路部分を「2階建て」にすることができれば、回路部分は画素部分とは独立に微細化を進化させて、高画質化や高機能化のために必要な大規模な信号処理回路もより低消費電力で搭載できるはずです。小型化と低価格化に留まらない可能性を秘めた構造案でした。
1カ月半ほどで積層型CMOSイメージセンサーの概念設計を決めた後、梅林は上長にプレゼンテーションを行い、無事、プロジェクト承認を受けました。
2008年8月、専任メンバー5人という小規模なチームを核に、積層型CMOSイメージセンサーの開発プロジェクトがスタート。概念設計までは比較的スムーズにたどり着いたものの、実際にそれを物理的に組み上げることが大きなチャレンジでした。結果的に、梅林らは1年半近く悩むことになるのです。
前進を阻む大きな原因になっていたのが、画素の層と回路の層、それぞれのウェーハの貼り合わせでした。
「貼り合わせ時には表面を真っ平にしなければなりません。スマートフォンの表面に保護フィルムを貼るイメージです。層の間に空気が入って泡ができないよう、きれいに貼り合わせないと駄目なのです」
ただし、非常に硬くて薄い板であるウェーハでは非常に困難なことでした。また、貼り合わせが少しでもずれると、上部の画素と下部の回路を接続するコンタクトの位置が外れてしまうため、イメージセンサーとして機能しなくなってしまいます。
その貼り合わせの精度について、梅林は、「直径120mくらいの規模の野球場がウェーハだとしたら、その大きさの野球場2つを1mmもずれないように重ね合わせなければいけないようなもの」と表現します。実際のウェーハでいうと、ズレは「2.5μm以内」に収めないと画が出ないため、これまで難易度の高い半導体製造に慣れた手練れであっても悩むほどの“超ウルトラC”でした。
大きなハードルを前に、梅林らが取り組んだことは極めてシンプル。チーム全員で「ウェーハのよい貼り方はないか」と考えて、それを実験し、出てきた結果を検証して、また実験を計画するという地道なPDCAサイクルをひたすら回しました。プロジェクトは当初、社内ではマイナーな扱いだったので、人やお金を割いてもらえず、小さなチームで淡々と実験を繰り返していましたが、途中から回路設計のエンジニアが参画してくれたり、プロセス設計のエンジニアは飽くなき挑戦を繰り返して手を尽くしてくれたりする中で、ようやく明るい兆しが見えてきました。
ところが、梅林のチームの経過に対する上からの期待と関心は徐々に高くなり、「2010年の春にパイロットラインで画出し検証するから、年内(2009年)には必ず貼り合わせを成功させてくれ」と、急に話が進み、タイムリミットはすぐ目の前まで迫っていました。
梅林チームは戸惑いながらもラストスパートをかけましたが、年内には間に合わず、上長には「年明けにはきっと貼り合わせます」と約束。もうそれ以上「待ってください」とは言い出せない空気でした。
積層型CMOSイメージセンサーの開発プロジェクトが立ち上がってから1年以上が経ち、事情を知らない社内の人からすれば、梅林らが一体何をしているのかまったく見えません。実際、職場では肩身が狭かったと言います。
「家族に対しては、何ともないフリをしながら、気が気でない年末年始を過ごしました。ずっとこのまま駄目で、春のデモも成功しなければ、会社を辞めるしかないのかなと。辛くて胃が重たかったです」
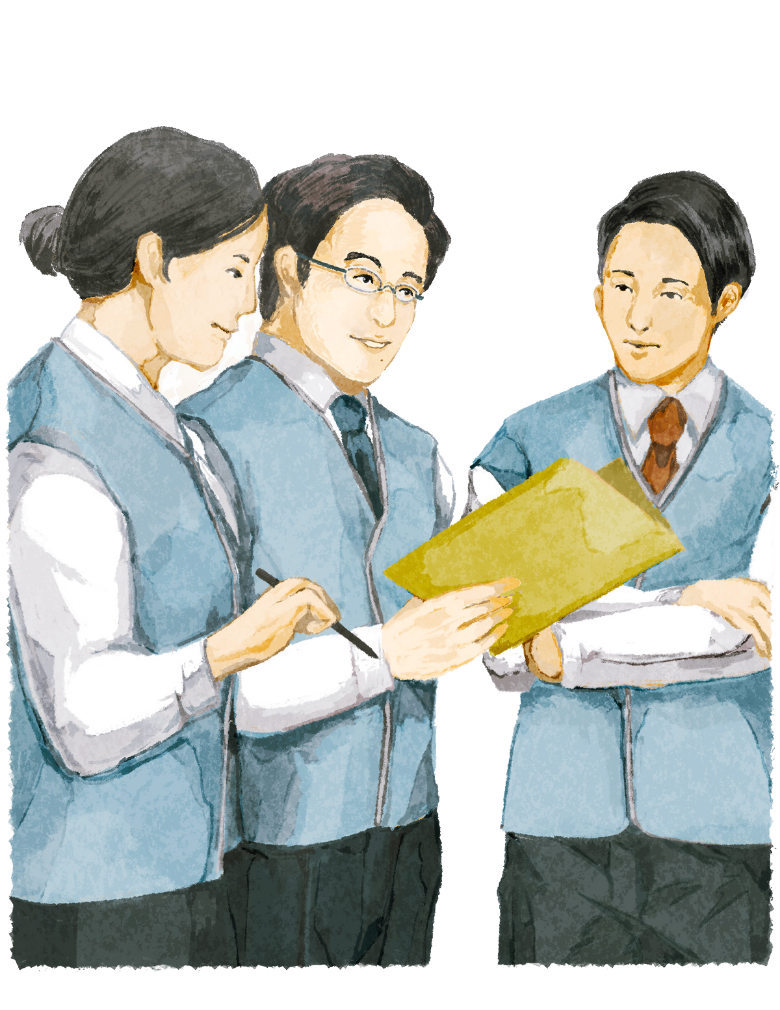
「梅林さん!!試作は何とか流せそうです!」
年は明けて、まだ不完全ではあるものの、ようやく試作流動できる程度の貼り合わせは可能になりました。但しウェーハの状態を確認しながら恐る恐るの流動です。気が気ではありませんでした。それでも何とか試作を流し切る事ができ、歩留りはボロボロでしたが、上下チップの電気的な導通を示す良品チップを取得する事ができました。こうして2010年3月に予定されていたデモは、白黒の画出ししかできなかったものの、乗り切ることができました。チップレベルの電気的な導通が取れた事で、梅林は技術的には積層構造を成り立たせる事はできると確信しました。
梅林らがカラーでの画出し検証を進めるのと並行して、社内は商品化に向かってアクセル全開で動き出し、ソニーの熊本テクノロジーセンターで量産にむけた試作が始まりました。熊本ででき上がったサンプルをもとに、再び社内デモを実施。当時の裏面照射型CMOSイメージセンサーにひけを取らない画質と明るさの画像、そしてチップの小ささを目の前に、その場にいた全員が驚きを隠せなかったと言います。
「積層型のチップを上から顕微鏡で覗くと、皆が『こんなに小さくて、しかも画素部分しかないのに、どうやって動いているの?』とビックリしていました。積層だから画素の下に隠れた回路部分が見えなかったわけです」
梅林が積層型のプロジェクトチームにやってきてから、実に3年9カ月。ついに積層型CMOSイメージセンサーは、2012年1月に開発発表され、8月の商品発表を経て、同年10月から出荷が始まりました。
「最初に搭載されたあるメーカーのタブレット製品に関する記事に、『積層型CMOSイメージセンサーを搭載』と書いてありました。嬉しくてね、躍起になって記事を保存しましたよ」
その後、積層型CMOSイメージセンサーは、ソニーモバイルコミュニケーションズ(現ソニー)のスマートフォンで、明暗差のあるシーンでも色鮮やかな動画撮影を可能にする「HDR(ハイダイナミックレンジ)ビデオ機能」など、撮影機能を向上させた「Xperia Z SO-02E」に実装されたことで話題に。それが起爆剤となってソニーの積層型CMOSイメージセンサーがほしいというメーカーからの声がどんどん大きくなっていきました。
「積層技術は秘密裏に開発されていたので、ソニーが発表して他社は驚愕したと思います。ただし、そう簡単に真似はできなかった。実際、他社から積層技術が出てきたのは2年後ですから。恐らくウェーハを貼るのが大変だったのではないかと思います。」
米Strategy Analyticsの調査によれば、2021年のモバイル用CMOSイメージセンサー市場は、前年比3%増の151億ドル規模に成長。ソニーセミコンダクタソリューションズがそのうちの45%を占め、世界トップシェアとなっています。
そして、2021年4月。梅林は、科学技術分野における発明・発見や、学術およびスポーツ・芸術文化分野における優れた業績を挙げた人に対して授与される紫綬褒章を受章しました。梅林らが開発した積層型CMOSイメージセンサーが、スマートフォンなど多くの製品に実装されて世の中に広まり、それが国民の利便性を向上させ、かつ日本の半導体産業を活性化させたという功績がたたえられたのです。
「あの時は、突然ふとうまくいったり、誰かがすっとやってきて助け舟をだしてくれたりで、何とか前に進んでいけて。普通では考えられないような、不思議なことが何回か起こって、多くの人に助けてもらいながら何とか成功までこぎつけました。」
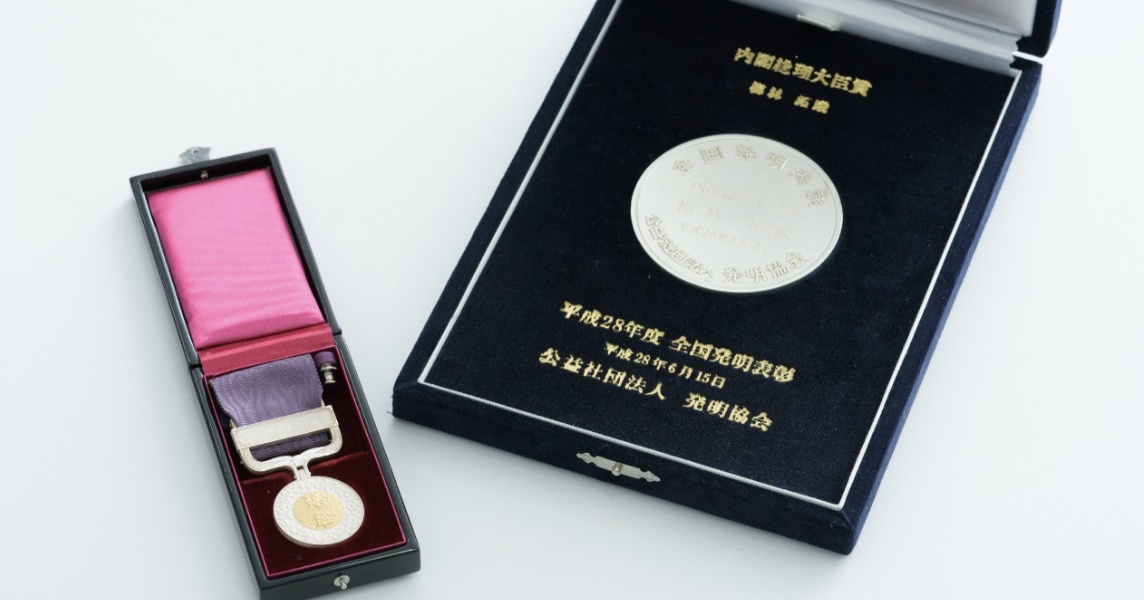
梅林はこのように開発当時のことを感慨深く振り返ります。
CCD時代、裏面照射型CMOS時代、そして積層型CMOS時代と、ソニーのイメージセンサーのエンジニアたちは、常に新しい世界を切り開こうとする信念の下、大きな成功をつかみ取りました。
そんな不屈のエンジニアたちの、イメージセンサーの高みをめざす挑戦は、まだまだ続いていくのです。